Bronze casting outsourcing: evaluate foundries and control your final patina
Thinking of outsourcing your bronze casting? This guide helps you pick the right foundry, negotiate flawless finishes, and keep full artistic control over the patina that will define your sculpture's mood for decades.
Why outsource bronze casting?
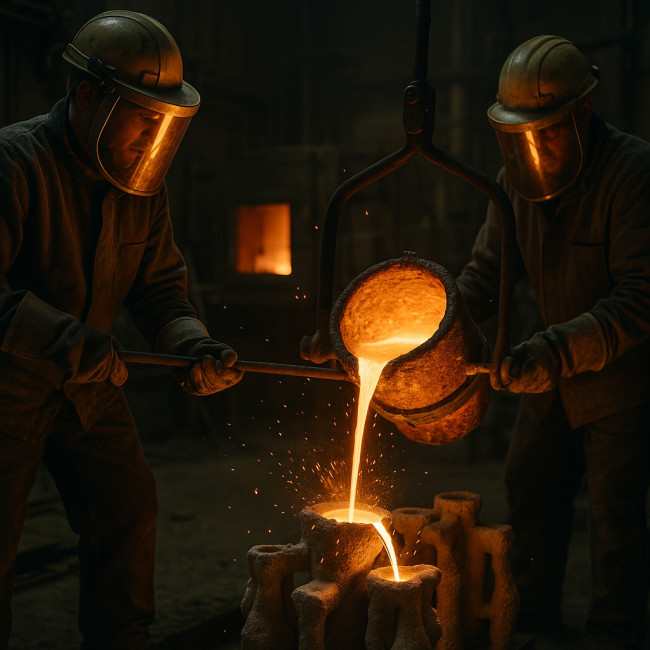
Foundries invest millions in furnaces, crucibles, and fume-extraction systems. Unless you run a high-volume studio, outsourcing lowers capital risk, shortens lead times, and lets you tap specialised surface treatments. You focus on concept and client relations while a partner handles melt temperatures, core vents, and finishing booths.
Key criteria to evaluate a bronze foundry
Alloy certification and traceability
Request recent batch certificates (EN 1982 or ASTM B584). They prove copper, tin, zinc, and lead ratios and reassure eco-minded collectors. For extra credibility, shortlist foundries that already supply eco-certified metal projects—you ride their audit trail.
Moulding and casting capabilities
- Lost-wax vs. sand: lost-wax delivers finer detail but costs 15-25 % more per kilo.
- Maximum pour weight: ensure the crucible fits your heaviest section to avoid risky weld-ups.
- Vacuum or centrifugal options: useful for jewellery-scale works needing zero porosity.
Surface finishing portfolio
Examine samples of chased seams, media-blasted textures, and colour patinas. A partner that operates an in-house metal finish library (article available soon) saves you extra freight and coordination headaches.
Project management and communication
Clear point-of-contact, bilingual staff, and digital approval loops reduce costly remelts. Many top foundries now share progress through secure dashboards such as Artfolio's craft-designers workspace, where you can comment on wax photos in real time.
Environmental and safety compliance
Check ISO 14001 and local workplace-safety records. Good ventilation and fume-scrubbers protect staff and your reputation.
In-house vs outsourced bronze casting
Factor | In-house | Outsourced |
---|---|---|
CapEx | €150 k-€500 k for furnace & extraction | None |
Unit cost (5 kg artwork) | €300-€350 | €190-€260 |
Lead time | Flexible but often slower without full-time staff | 3-6 weeks |
Finish range | Limited to on-site skills | 15+ patinas, media blasting, CNC chasing |
Scalability | Equipment bottlenecks | Multi-shift foundries scale fast |
Cost benchmarks by region
Global rates vary sharply. The bar chart below compares average 2023 bronze casting prices for a 10 kg sculpture (lost-wax, raw metal finish). Use it to calibrate quotes and spot outliers.
Source : Foundry-Planet 2023 Cost Survey
Seven-step process to keep control of your final patina
- Define the chemical recipe early. Supply the foundry with a written formula (e.g., Cupric nitrate 30 g/l + ferric chloride wash) and colour swatches.
- Book a test plate. Ask for a 10Ă—10 cm bronze plate treated with your recipe. Approve by video under neutral light.
- Lock the surface prep. Specify grit size, brushing direction, and any sand-blasting before patination.
- Schedule patina while metal is warm. Many greens and browns develop best at 90-120 °C. Confirm furnace access.
- Record time-temperature curves. A simple infrared gun and stopwatch give repeatable data for future editions.
- Seal smart. Decide between microcrystalline wax (interior) or acrylic lacquer (outdoor) and note brand names.
- Ship with handling notes. Include humidity limits and glove requirements to avoid fingerprints during transit. See our shipping safeguard guide.
Common pitfalls and how to avoid them
- Pinholes after chasing: insist on X-ray or dye-penetrant testing for casts over 20 kg.
- Colour drift between editions: archive patina data sheets and insist on batch-specific photos.
- Hidden duty fees: agree on Incoterms DDP to avoid surprise VAT and customs paperwork.
- Mismatched shrinkage: ask for digital 3D scans of waxes to confirm dimensions before casting.
FAQ
- How many editions can a silicone mould support?
- Silicone rubber withstands 25–30 wax pulls before detail loss. Plan extra moulds for larger runs.
- Can I outsource just the rough cast and finish it myself?
- Yes. Negotiate a “pour-only” rate and clarify gate removal points so you can chase seams in-house.
- What is a realistic lead time for a 1 m bronze figure?
- For lost-wax, budget six weeks: two for mould and wax, two for ceramic shell, one for metal pour, one for patina and seal.
- Does outsourcing void the “hand-made” claim?
- No. As long as you oversee decisions and sign each artist proof, collectors still regard the piece as hand-made.
Quick quiz: Are you ready to brief a foundry?
Take control of your next pour
Outsourcing bronze casting need not dilute your artistic vision. Evaluate foundries with the criteria above, lock your patina recipe early, and document every step. The result: museum-grade bronzes, delivered on time, at costs that keep your studio profitable.
Ready to brief a foundry? Download our free checklist and join hundreds of sculptors who reduce revisions by 40 %.