Custom tableware briefs: glaze durability specs architects should request
You have one chance to specify custom tableware that survives years of room-service trolleys, rooftop restaurants and high-traffic cafés. This guide shows architects exactly which glaze durability metrics to demand, how to phrase them in a brief, and where to spot red flags before signing off on the final firing.
Why glaze durability is a non-negotiable in hospitality design
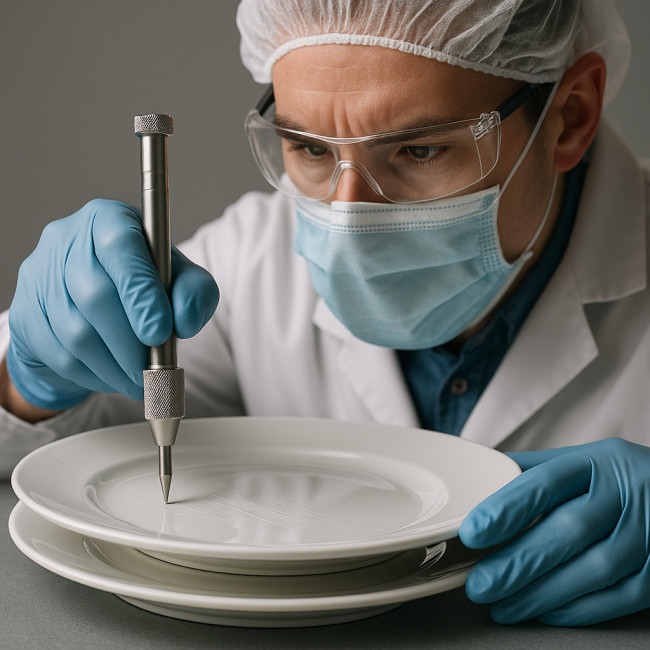
Glaze durability dictates how well plates, cups and serving pieces resist scratches, stains and sudden temperature swings. When the finish fails, the venue loses both aesthetics and hygiene points—often within the first season of use. By locking in clear performance numbers now, you avoid costly replacements and protect the brand image of every project.
Core durability metrics to include in your brief
Metric | Minimum Spec to Request | Why It Matters |
---|---|---|
Mohs hardness | ≥ 7 | Prevents visible cutlery scratches on glossy whites and colour-saturated glazes. |
Dishwasher cycle resistance | 1,000 cycles at 75 °C with ΔE colour change < 1 | Keeps hues consistent under commercial cleaning chemicals. |
Thermal shock tolerance | ≥ 180 °C differential (e.g., ‑20 °C to 160 °C) | Prevents hairline cracks when plates move from freezer to salamander. |
Chemical resistance | No visible etching after 24 h citric acid soak (3 %) | Stops matte spots from acidic foods and cleaning agents. |
Lead & cadmium leach | Below ASTM C738 detection limits | Meets global food-contact safety rules and avoids import delays. |
Translate numbers into a rock-solid specification
- Name the standard. Reference ASTM C501 for abrasion or ISO 10545-9 for thermal shock instead of vague “commercial grade” wording.
- Add test method details. State cycle counts, temperature ramps and colour-difference thresholds.
- Define sample size. Require at least 10 random pieces per glaze colour for each test to avoid cherry-picking.
- Request certification copies. Certificates must include the independent lab's accreditation number and test date.
- Agree on remediation. Include a clause for free replacement if more than 2 % of a production batch fails within the first year.
Testing laboratories and standards architects should cite
Independent labs such as Lucideon (UK), SGS (global) and TĂśV SĂĽd run complete ceramic durability suites. Pair them with the correct norms to avoid supplier pushback:
- ISO 10545-13: Chemical resistance.
- ASTM C650: Household chemical etch resistance.
- ASTM C356: Glass-ceramic thermal shock.
- ASTM C501: Surface abrasion—ideal for matte glazes.
When a maker proposes their own in-house test, ask for side-by-side data from an accredited lab listed above.
Budget versus longevity—find the sweet spot
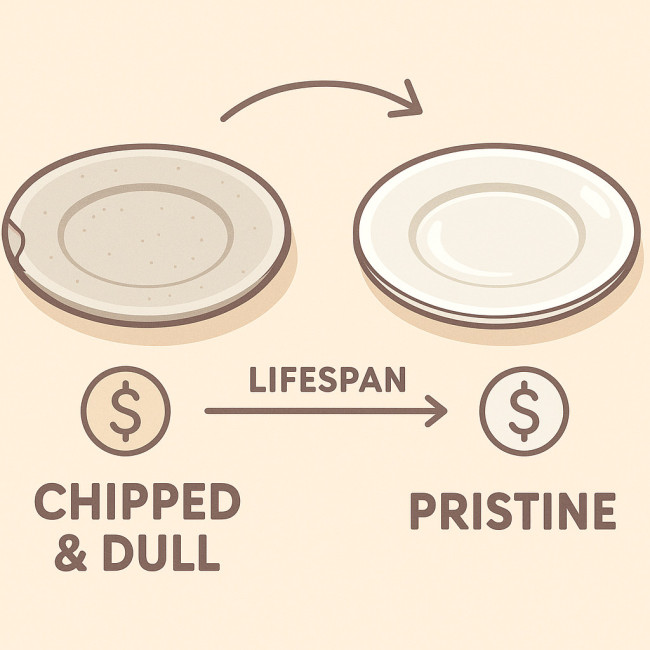
Raising Mohs hardness from 6 to 7 adds roughly €0.30 per plate at scale, yet triples scratch-free lifespan in busy banqueting venues. The return on investment outpaces most other front-of-house fixtures. For more ways to evaluate long-term value, compare capacity metrics using our deep dive on studio capacity metrics (article available soon).
Common pitfalls to avoid
- Confusing clay body with glaze. A vitrified porcelain base still needs a high-hardness topcoat.
- Ignoring colour additives. Cobalt-rich blues increase hardness; copper reds lower it—specify by colour if your palette varies.
- Skipping edge-chip tests. High hardness doesn't stop rim fractures from metal-to-ceramic knocks.
- Accepting “commercial dishwasher safe” language. Demand numeric cycle counts and temperature settings instead.
Workflow tips when glazing remotely
If your project involves an overseas kiln, use digital approval loops to lock sheen and hue before firing. Our guide on remote glazing approvals shows how architects maintain colour accuracy across time zones.
Case study link to vetted craft designers
Need a shortlist fast? Browse award-winning craft designers already fluent in hospitality-grade testing and documentation.
Quick self-check quiz
FAQ
- Can I mix matte and gloss glazes in one dinner set?
- Yes, if each glaze independently meets the hardness, chemical and dishwasher specs listed above. Request separate certificates for every finish.
- Is a higher Mohs value always better?
- Beyond 8, plates may become brittle under edge impacts. Balance scratch resistance with chip tolerance by running both ASTM C501 and ISO 10545-9 tests.
- How often should hospitality venues replace tableware?
- With the durability targets in this article, replacement cycles stretch to 5–7 years instead of the typical 2–3 years for standard stoneware.
Ready to specify flawless glaze durability?
Insert the metric table into your next tender, attach the relevant ASTM or ISO methods, and ask suppliers for third-party certificates up front. You will save budgets, reduce maintenance calls and heighten the dining experience—project after project. Need help auditing a ceramist's proposal? Explore our procurement roadmap or double-check sustainability labels before you sign.
Take action: Download the editable spec sheet now and forward it to every shortlisted maker before the next design review.